
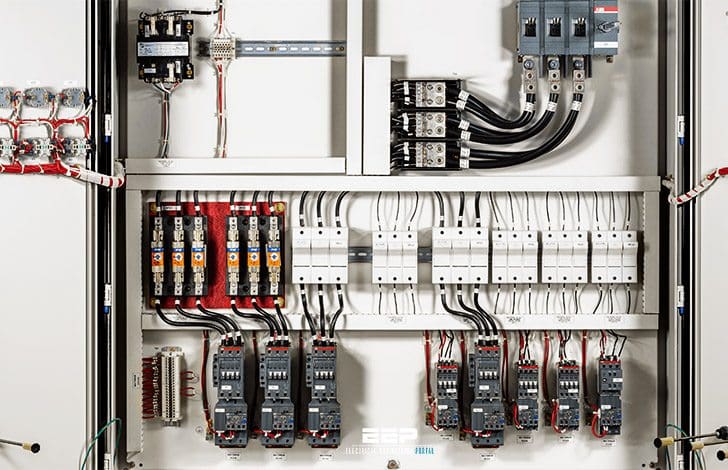
- #Industrial control circuit design software how to#
- #Industrial control circuit design software software#
- #Industrial control circuit design software plus#
The Viterbi/Complex Math Unit (VCU-I) speeds complex math operations commonly found in encoded applications.
#Industrial control circuit design software plus#
The F28004x is based on TI’s 32-bit C28x CPU running at 100 MHz, plus specialized accelerators for several algorithms that are common in real-time motor control.įor instance, the trigonometric math unit (TMU) enables fast execution of algorithms with trigonometric operations such as transforms and torque loop calculations. (Source: TI Microcontrollers: C2000 Piccolo 32-bit microcontrollers) The Piccolo F28004x contains many specialized blocks for motor control. The result is a dual-axis servo drive controller on a single chip that reduces BOM cost while delivering a high level of motion-control performance.Ģ. 2) are the newest members of the Piccolo portfolio these devices incorporate many of the features of the high-end Delfino F2837x floating-point performance MCUs plus added features for ac drives and servo applications.
#Industrial control circuit design software how to#
Piccolo F20004x Two-Axis Servo ControllerĪlthough designers are always pushing the envelope in search of ever-increasing levels of performance, a more germane challenge for many applications is how to implement multi-axis servo motor control in the most cost-effective manner. The Delfino line of four devices offers premium performance and expanded feature sets for the most advanced closed-loop control applications. The Piccolo line contains six devices and offers cost-effective performance with high levels of integration for a broad set of closed-loop control applications. Texas Instruments’ C2000 is a family of high-performance 32-bit MCUs purpose-built for real-time control in demanding applications such as electric vehicles, industrial drives, and digitally controlled power conversion. Switching to a single dedicated device reduces bill-of-materials (BOM) costs, cuts development time, and provides a single point of contact to help with tricky design issues.Ĭ2000: An MCU Family Designed for Real-Time Control For more information, consult this detailed discussion of SoC-vs.-FPGA design tradeoffs.Īs digital control became the preferred approach, MCU manufacturers began introducing system-on-chip (SoC) products that included the standard motor-control building functions, flexible peripherals that allowed for modifications, plus the ability to make changes using the standard development environment and programming languages such as C. Programming the FPGA or making updates adds considerable cost and time to the development cycle. However, these devices, while certainly fast, are expensive and notoriously hard to program because they require an intimate knowledge of the underlying hardware structure and a dedicated set of development tools.


Options include a field-programmable gate array (FPGA) or a complex programmable logic device (CPLD). Consequently, designers added external logic devices to handle these functions.
#Industrial control circuit design software software#
When designers began designing servo-motor controllers based on digital technology, they found that the available off-the-shelf microcontrollers (MCUs) couldn’t support some of the specialized requirements, such as intricate protection schemes for the power drivers, complex encoder interfaces, or current loops that were too fast for a software implementation. Since some drive electronics functions-and their costs-can be shared across multiple axes, it makes sense to consider servo drives that can support two or more axes instead of the traditional one-drive/one-motor approach.ĬOTS Motor-Drive Solutions Lower Costs, Simplify Design Most industrial automation machines have multiple motor axes, so the cost per axis is a suitable measure. However, given the progress already made in digital drive control performance, the greater challenge today is reducing the cost of standard motion performance applications, rather than the maximum attainable control bandwidth for speed and position loops. Some applications will always require the highest performance and highest precision. In this fast-moving market, servo-drive manufacturers are always looking for improvements in performance, connectivity, ease of use, and cost. (Source: “Delivering the next generation of low-cost, dual-axis servo drives,” Electronic Design). Precision servo drives are ubiquitous on the factory floor.
